Introduction
Conveyor systems are widely used in various industries to transport materials and goods efficiently and quickly. These systems rely on control cables to ensure proper operation and smooth functioning. Control cables play a crucial role in managing the speed, direction, and overall performance of conveyor systems. In this article, we will explore the importance of conveyor system control cables, their key features, applications, and best practices for maintenance and installation.
Importance of Conveyor System Control Cables
Control cables are essential components of conveyor systems as they enable operators to manage and control the movement of materials along the conveyor belt. These cables transmit signals from the control panel to the motors, sensors, and other devices that regulate the speed, direction, and positioning of the conveyor system. By utilizing control cables, operators can ensure precise and reliable operation of the conveyor system, leading to increased efficiency and productivity.
Key Features of Conveyor System Control Cables
Conveyor system control cables come in various types and configurations to suit different applications and requirements. Some of the key features of these cables include:
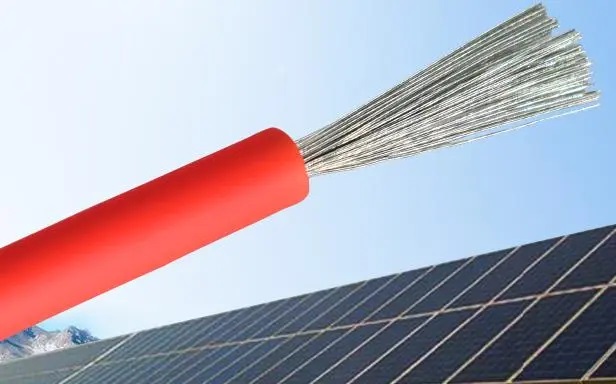
1. Durability: Control cables for conveyor systems are designed to withstand harsh industrial environments, including exposure to extreme temperatures, moisture, chemicals, and mechanical stress. They are typically constructed using high-quality materials such as PVC, polyurethane, or rubber to ensure long-lasting performance.
2. Flexibility: Control cables need to be flexible to accommodate the dynamic movements of the conveyor system. Flexible cables allow for smooth operation and prevent kinks or tangles that can disrupt the flow of materials along the conveyor belt.
3. Shielding: To ensure reliable signal transmission and protection against electromagnetic interference (EMI) and radio frequency interference (RFI), control cables are often equipped with shielding layers. Shielded cables help maintain signal integrity and minimize the risk of signal loss or distortion.
4. Temperature Resistance: Conveyor system control cables must be able to withstand a wide range of temperatures, from freezing cold to extreme heat. Heat-resistant cables are essential for applications where the conveyor system operates in high-temperature environments such as foundries or baking facilities.
Applications of Conveyor System Control Cables
Conveyor system control cables find a wide range of applications across various industries, including:
1. Manufacturing: In manufacturing facilities, conveyor systems are used to transport raw materials, components, and finished products between different stages of the production process. Control cables play a critical role in ensuring the efficient and seamless operation of these systems.
2. Warehousing and Distribution: Conveyor systems are commonly used in warehouses and distribution centers to automate the movement of goods and packages. Control cables help manage the flow of materials, sort items, and control the speed and direction of the conveyor belts.
3. Mining and Quarrying: In the mining and quarrying industry, conveyor systems are utilized to transport bulk materials such as coal, ore, and aggregates. Power Cable For Sale are essential for regulating the movement of materials along the conveyor belts and ensuring safe and efficient operation in challenging environments.
4. Food and Beverage: Conveyor systems are widely employed in the food and beverage industry for handling and processing food products. Control cables play a crucial role in maintaining hygiene standards, controlling the speed of conveyors, and ensuring the safe transportation of perishable goods.
Best Practices for Maintenance and Installation of Conveyor System Control Cables
Proper maintenance and installation of conveyor system control cables are essential to ensure optimal performance and longevity. Here are some best practices to follow:
1. Regular Inspection: Conduct routine inspections of control cables to check for signs of wear, damage, or corrosion. Replace any damaged cables immediately to prevent disruptions in the conveyor system's operation.
2. Proper Installation: Follow the manufacturer's guidelines for installing control cables to ensure correct placement and secure connections. Avoid sharp bends or twists in the cables, as this can lead to signal loss or cable breakage.
3. Cable Management: Keep control cables organized and properly secured to prevent tangling or interference with other components of the conveyor system. Use cable trays, conduits, or cable ties to maintain a neat and tidy cable layout.
4. Environmental Protection: Protect control cables from exposure to moisture, chemicals, and abrasive materials that can degrade the cable insulation and lead to malfunctions. Use cable glands, protective covers, or conduits to shield cables from environmental hazards.
5. Training and Documentation: Provide training for operators and maintenance personnel on the proper handling and care of control cables. Keep detailed records of cable installations, maintenance activities, and replacement schedules to track the performance of the cables over time.
Conclusion
In conclusion, conveyor system control cables are essential components that play a critical role in the efficient and safe operation of conveyor systems across various industries. By understanding the key features, applications, and best practices for maintenance and installation of control cables, operators can enhance the performance and reliability of their conveyor systems. Investing in high-quality control cables and following proper maintenance procedures will help ensure the smooth functioning of conveyor systems and contribute to increased productivity and safety in industrial environments.